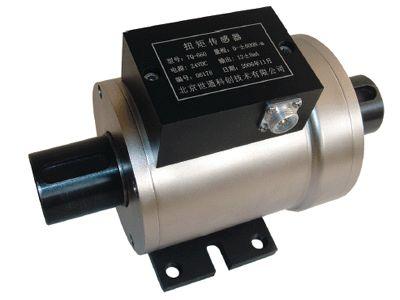
功率和功耗是测量发电厂电能生产的重要配对值:功率可以非常容易地通过发电机的输出测量.但是,效率程度-特定时间发电机的有效功率和驱动功率的比值的测量非常困难。
有很多方法可以用于测量燃料质量流。但是燃料质量流直接测量是很不精确地。一系列的因素会影响燃料参数和使用的燃料类别,带来很大的不确定性。实践中,燃料的质量流往往通过以前测量的标定值或通过模拟软件来间接确立。
另外一个测量驱动动力的方法是测量在驱动器和发电机之间轴系的扭矩。这样就可以根据速度来计算出驱动输出。通过驱动扭矩产生的驱动轴扭矩可以进行测量.一系列的方法可以用于此目的。但是,这有一个通病:都不是直接测量扭矩。而是通过关于扭矩的参数和随后的计算得出的。计算用的参数具有很大的公差,导致了扭矩测量的不确定性。
更好的方法是通过测量驱动轴表面的应力来测量扭矩。应变计安装在轴的表面,然后链接到桥路放大器。测量信号和测量桥路的电源通过 telemetry 系统在定子和转子之间进行无线传输。这个方法可以获得非常精确地测量值。但是接下来进行扭矩值计算时会存在 3到 5%的误差。原因是:以上提及的参数公差将会被带入计算。这个理论也有一定优势-例如,现存的系统在任何时候都可以进行翻新。但是对于新的发电厂,扭矩参数的不确定性无法满足需求。
以上方法的不确定性可以通过对驱动轴或部分驱动轴标定来提高参数的精度。通过标定机对驱动轴不断增加负载来进行标定。相应的信号进行测量并记录。标定过程可以在现场进行。但是现场标定费用更高,而且现场环境更复杂。在实验室标定将能够获得更高的精度。另外,在某些情况下不适合标定机进行工作,或者元件的尺寸以及最大扭矩的限制都会带来很大的困难。
…现在,不确定性已不复存在–可以更简单更精确测量扭矩以上描述的困难可以非常容易避免。可以在电厂设计时考虑扭矩测量功能:在驱动链上直接安装元件,将其一起旋转或考虑将其做为驱动链功能。扭矩传感器已经在实验室进行了标定并带有标定证书。其非常容易进行安装,替换并进行重新标定.
依赖 telemetry 系统的扭矩传感器,可以提供动态扭矩信号,信号带宽最大到 6kHz.其用于发电厂具有多种优势:
高精度,高效测量(监控)
燃料消耗和优化
无需其他传感器进行扭矩震动分析
检测扭矩特性曲线变化
服务周期修理或修正判断
更短的信号延迟
过载时快速调整和限制
容易安装
安装,标定更简单
ATEX 认证,可用于可能爆炸环境
ABS 或其他相同认证,可用于造船